汇总众多学者几十年的研究结果,微弧氧化技术的工艺优点可归纳为以下两 点。首先,清洁处理的理论可行性满足了轻量化制造的环保要求。轻量化制造的主 耗材为铝、镁等轻金属。微弧氧化处理既与电镀锌等消耗性阴极处理不同,可用非 消耗性的不锈钢作阴极,避免了重金属离子从阴极溶入并随废水流出污染环境; 又与电镀硬铬和重(或硬)阳极氧化等依靠消耗溶液中溶质元素在被处理样品表 面形成保护膜层的工艺不同,微弧氧化处理主要在铝、镁等轻合金表面生成金属 自身氧化物的陶瓷层,理论上属不消耗溶质元素的处理工艺。因此该工艺可以被 视为既不消耗阴极又基本不消耗电解液溶质元素的清洁处理。
其次,生成物的陶瓷属性满足了轻量化制造的表面性能要求。铝、镁合金因使用环境不同而需赋予不同的表面性能。经微弧氧化处理的铝、镁合金,因其表 面生成一层与基体以冶金方式结合的氧化铝或氧化镁为主的陶瓷层,陶瓷质的高 硬度、高阻抗和高稳定性满足镁合金抗高温腐蚀、连接(电偶)腐蚀、擦伤腐蚀及铝合金防海水腐蚀、高温热蚀和改善耐磨等性能要求。经微弧氧化处理的镁合 金制品,不仅抗蚀性能优异,更由于氧化镁陶瓷层的高阻抗特性而避免了镁合金与 其它金属间的高温“连接腐蚀”,解决了镁合金在汽车等交通行业应用的表面保护技术难题。
微弧氧化陶瓷层具有特殊的结构,图 1 是镁合金微弧氧化陶瓷层的表面及截 面形貌。从截面结构可看出陶瓷层与基体以冶金型微熔过渡区连接,层内组织致密 无穿孔;表面形貌可看到 um 级盲孔微区均匀分布,既利于连续油膜的形成降低 摩擦系数,同时又可增强后续涂装的其附着力。
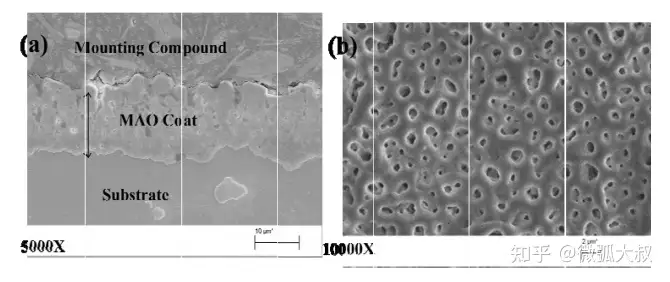
另外,将微弧氧化技术与其它表面处理工艺及所得膜层的性能进行对比,综合起来,微弧氧化技术及微弧氧化陶瓷层还具有以下特点:
(1)孔隙率低,从而提高了陶瓷层的耐腐蚀能力;
(2)含高温转变相,使陶瓷层硬度高、耐磨性好;
(3)陶瓷层在基体原位生长,膜层与基体结合紧密,不易脱落;
(4)通过改变工艺条件,可以很方便地调整陶瓷层的微观结构、特征和获得 新的微观结构,从而可实现陶瓷层的功能设计;
(5)能在试件内外表面生成均匀陶瓷层,扩大了微弧氧化的适用范围;
(6)陶瓷层厚度易于控制,提高了微弧氧化的可操作性;
(7)处理效率高:一般阳极氧化获得 50μm 左右的陶瓷层需要 1~2h,而微 弧氧化只需 10~30min;
(8)操作简单,不需真空或低温条件,前处理工序少,性能价格比高,适宜 于自动化生产;
(9)对材料的适应性宽,除铝、镁合金外,还能在 Ti、Zr、Ta、Nb 等金属及 其合金表面生长陶瓷层;
(10) 微弧氧化技术还具有工艺简单,对环境污染小,具有清洁工艺之称。
铝、镁合金经微弧氧化处理后形成陶瓷层表面的多孔特征,在恶劣环境下常 发生点蚀,难以满足实际工程应用的要求。然而,多孔结构的陶瓷层却很好的满足 了后续涂装工艺对基材表面的要求(均匀、多孔)。将不需前处理的微弧氧化与 静态防护性能优异的有机物涂装技术相结合,在铝、镁合金表面制备具有高性能、 多用途的陶瓷有机复合涂层,所得复合涂层的性能明显优于单一微弧氧化或传统涂 装工艺。微弧氧化复合处理(Micro-arc Composite Ceramic,MCC)技术具有工艺 简单、环保、无排放,处理效率高,涂层综合性能优异,以及对材料的适应性强 (复杂构件或深孔管件)等优点,已成为业界认可的铝、镁合金“环保型” 表面处 理技术。
采用中性盐雾试验表征不同处理铝、镁合金的耐蚀性,以样品表面出现腐蚀 点所消耗的时间为评判依据,测试结果如图 2 所示。从图 2 中可以看到铝合金微 弧氧化处理后耐盐雾试验测试达 5000 小时,耐蚀性较传统工艺提高至少 4 倍; 镁合金经微弧复合处理处理后耐盐雾试验测试也能够达到 2000小时,远大于 500 小时的测试国标要求。
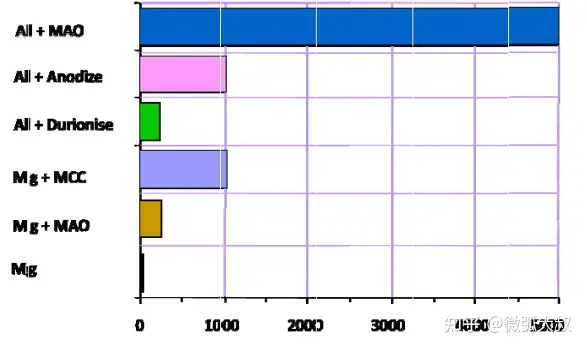
经过微弧氧化处理的铝、镁和钛等轻合金,陶瓷层的硬度与传统工艺所得涂 层相比也有明显提高。图 3 是不同处理铝、镁和钛合金的显微硬度测试结果,可 以看出镁、钛等合金经微弧氧化处理后的维氏硬度能够达到 600HV,与基体相比 提高明显。铝合金经微弧氧化处理后维氏硬度能够达到 1800HV,远优于电镀硬 铬处理(400HV)和基体。
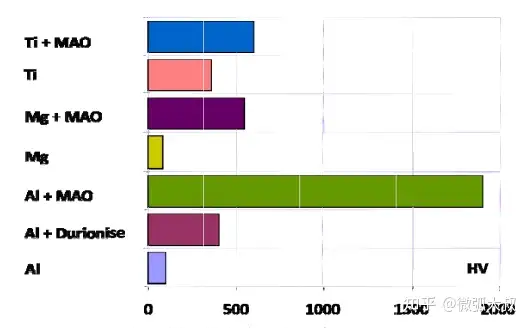
铝合金经微弧氧化处理后其维氏硬度显著提高,因此陶瓷层耐磨性与传统表 面处理工艺所得的涂层相比也有很大提高。微弧氧化陶瓷层与目前铝合金气缸体内表面常用的电镀硬铬和磷钒铜铸铁进行相同摩擦条件下的磨损实验(滑动摩擦, 载荷 50N,石蜡润滑),实验结果如图 4 所示。在前 15h 的磨损过程中,陶瓷层 的磨 损量随时间呈缓慢上升趋势,磨损15h 后趋于稳定;电镀硬铬在约 23h 内表现出较 好的耐磨性,磨损量小于微弧氧化陶瓷层,但在 23h 后,磨损量随时间而迅速增加, 呈线性上升关系,从其磨损表面观察到部分镀铬涂层已被磨掉,呈现 出磨损失效现 象;磷钒铜铸铁在 20h 内磨损量随时间显著增加,后期磨损量随时间变化缓慢,但 仍有上升趋势,尽管磷钒铜铸铁在 20h 以后磨损率降低,但总磨损量较大,约为微 弧氧化陶瓷层总磨损量的 5 倍。综合来看,润滑条件下铝合金微弧氧化陶瓷层的耐 磨性能最好。
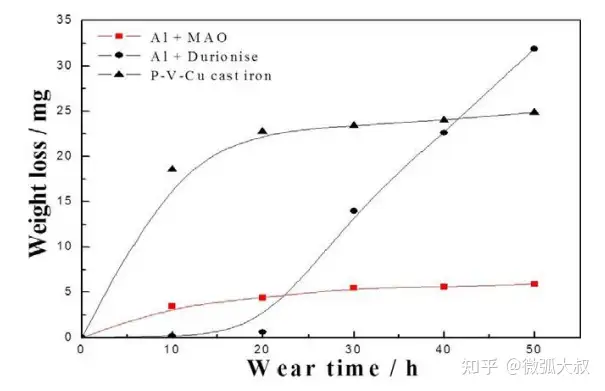
根据 GB/T1720-89 划圈法测试镁合金表面微弧复合膜层的结合力。将样板固定在一个可以移动的平台上,在平台上移动的同时,作圆圈运动的唱针划透漆膜, 并能划出重叠圆滚线的纹路,从圆滚线的纹路中观察漆膜的破坏位置,以判断附着 力的等级。镁合金直接电泳、化学转化电泳及微弧电泳的结合力测试结果如图 5。镁 合金直接电泳膜层的附着力等级为 4 级,化学转化/电泳复合膜层的附着力 等级为 2 级,微弧氧化/电泳复合膜层的附着力等级为 1 级。
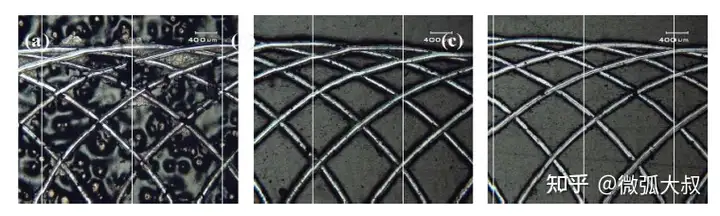
采用中性盐雾试验表征镁合金与铜的连接腐蚀性能,以表面出现腐蚀点所消 耗的时间为评判依据,测试结果如图 6 和图 7 所示。从图 1 中可以看到镁合金 MAO 处理后在盐雾试验 48 小时即在连接处出现腐蚀,至 144 小时出现严重腐蚀。 从图 2 中可以看到镁合金 MCC 处理后经过 120 小时盐雾试验,连接处未发现腐 蚀现象。结果显示微弧复合处理处理能够避免镁合金与铜的连接腐蚀。
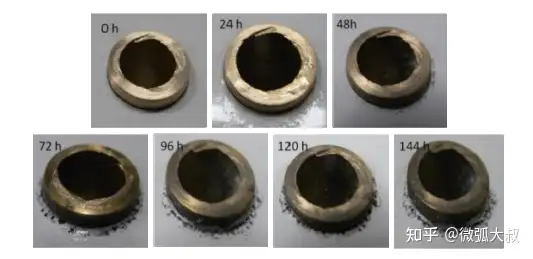
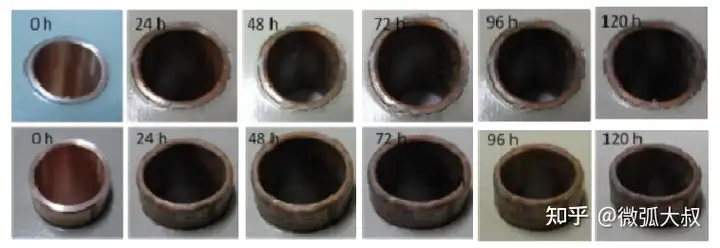
镁合金耐蚀性差成为其在汽车行业推广应用的瓶颈,选择合适的表面处理技术能够大幅度提高其使用寿命。在镁合金汽车零部件表面设计并制备微弧复合膜 层,按照汽车行业表面防护涂层评判依据,从耐蚀性(铜加速乙酸盐雾腐蚀试验, Cass Test),抗擦伤性(飞石冲击试,Stone Impact Resistance Test),环境稳定性 (热冲击试验,Thermal Shock Test),耐用性(磨损试验,Abrasion Resistance Test) 以及涂层结合力(附着力试验,Tape Adhesion Test)等方面对防护涂层进行综合 评价,经专业机构测试结果表明 MCC 处理镁合金能够满足标准要求(图 8), 进而奠定镁合金在汽车行业推广应用的理论和试验基础。
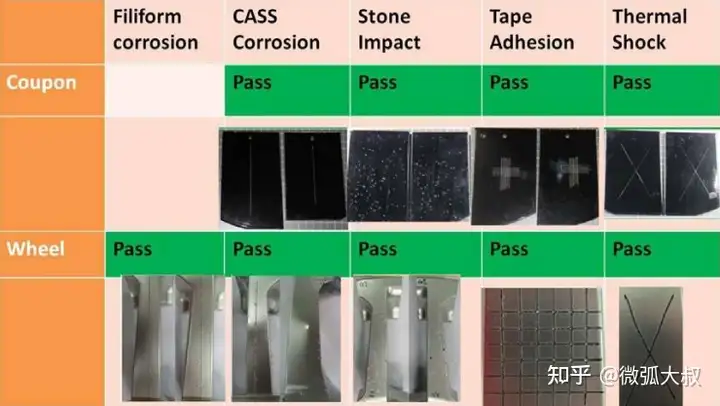